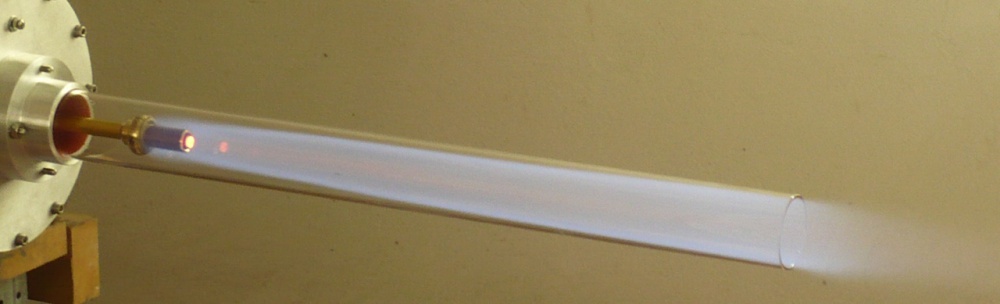
PROTOTYPE AND TEST
The 130KW Bruxin pre-mixed burner has been realized in a single working prototype after about 12 months of development and, following the numerous tests carried out, it has the following important advantages:
High and concentrated power
High yield
Low harmful gas emissions
Adjustable and versatile use
Compact and simple construction
Economical production
PRESENTATION AT THE POLITECNICO DI MILANO
Considering the remarkable and innovative results brought by our prototype, also in considering patentability, we decided to submit it to a careful analysis by the Politecnico di Milano. The Bruxin pre-mixed burner was therefore analysed by engineer Giulio Solero of the Department of Energy, whose report's conclusions are literally quoted below.
The 130KW Bruxin pre-mixed burner has been realized in a single working prototype after about 12 months of development and, following the numerous tests carried out, it has the following important advantages:
High and concentrated power
High yield
Low harmful gas emissions
Adjustable and versatile use
Compact and simple construction
Economical production
PRESENTATION AT THE POLITECNICO DI MILANO
Considering the remarkable and innovative results brought by our prototype, also in considering patentability, we decided to submit it to a careful analysis by the Politecnico di Milano. The Bruxin pre-mixed burner was therefore analysed by engineer Giulio Solero of the Department of Energy, whose report's conclusions are literally quoted below.
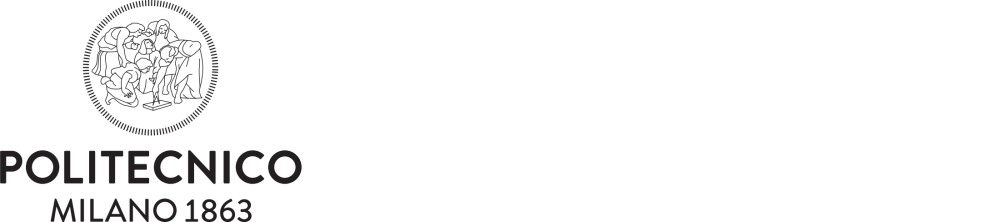
CITATION OF THE CONCLUSIONS OF THE REPORT
It can be seen that the burner has many advantages associated with both simplicity of construction and high efficiency and reduced environmental impact. On the basis of my personal experience, I believe I can highlight the following innovative aspects, compared to the fleet of combustion equipment currently in use:
The burner under examination combines the advantages of lean premixed combustion with a high stability connected both to the swirl motion given to the premixed current and to the presence of the stabilization body (generally, the swirl motion is used in case of diffusive combustion).
Within the operating range, the burner is able to operate with high efficiency ("cold" confinement tube and consequent reduction of heat loss during operation and periodic on/off) and reduced environmental impact (NOx emission levels typical of a low emission burner).
The flame has an intense blue colour, a clear sign of "clean" combustion without formation of CO, unburnt or particulate matter. In fact, measurements carried out on the polluting emissions from this flame have so far recorded in a first test NOx values (expressed as mg/Nm3 of NO2 at 3% O2) between 80 and 50, with negligible CO emissions (i.e. below the detection limit of the measuring instrument).
The low polluting emissions can be justified by observing that the morphology of the flame under examination can be assimilated to that of an inverse Bunsen cone, in which the flame front is locally "cooled" by the fresh mixture that invests it, contributing to the reduction of the formation of NOx - below 10 PPM - thermal due to the "cooling" and the local leaning operated by the mixture towards the flame front itself.
The use could be advantageous in applications requiring high local thermal power (e.g.: thermal cutting, material heat treatment, furnaces, dryers, ladle heating), but it is suitable for a large number of other uses.
The burner has a high simplicity of construction, with a positive impact on possible future production and maintenance costs.
It can be seen that the burner has many advantages associated with both simplicity of construction and high efficiency and reduced environmental impact. On the basis of my personal experience, I believe I can highlight the following innovative aspects, compared to the fleet of combustion equipment currently in use:
The burner under examination combines the advantages of lean premixed combustion with a high stability connected both to the swirl motion given to the premixed current and to the presence of the stabilization body (generally, the swirl motion is used in case of diffusive combustion).
Within the operating range, the burner is able to operate with high efficiency ("cold" confinement tube and consequent reduction of heat loss during operation and periodic on/off) and reduced environmental impact (NOx emission levels typical of a low emission burner).
The flame has an intense blue colour, a clear sign of "clean" combustion without formation of CO, unburnt or particulate matter. In fact, measurements carried out on the polluting emissions from this flame have so far recorded in a first test NOx values (expressed as mg/Nm3 of NO2 at 3% O2) between 80 and 50, with negligible CO emissions (i.e. below the detection limit of the measuring instrument).
The low polluting emissions can be justified by observing that the morphology of the flame under examination can be assimilated to that of an inverse Bunsen cone, in which the flame front is locally "cooled" by the fresh mixture that invests it, contributing to the reduction of the formation of NOx - below 10 PPM - thermal due to the "cooling" and the local leaning operated by the mixture towards the flame front itself.
The use could be advantageous in applications requiring high local thermal power (e.g.: thermal cutting, material heat treatment, furnaces, dryers, ladle heating), but it is suitable for a large number of other uses.
The burner has a high simplicity of construction, with a positive impact on possible future production and maintenance costs.